
Western Falcon Energy Services
Humble, Texas, United States
Western Falcon Energy Services
!
Our Patented Liner Technology... Increases Tubular Runlife. Reduces Costly Workovers.
About Western Falcon Energy Services
Western Falcon was established in 1992 in Odessa, Texas and offered Polycore HDPE liner primarily used for corrosion protection in water injection and disposal wells. In 1994, the first string was deployed in a beam pumped well to eliminate rod on tubing well failures. Since then, Western Falcon thermoplastic liners have proven successful in reducing tubing failure and workover costs.
In August 2000, Conestoga Supply Corp. purchased Western Falcon and focused on expanding the applications of thermoplastic liners. Western Falcon, has been heavily involved in research and development focusing on new thermoplastic materials and additional applications other than injection, disposal, flowlines, beam pumped and PC pumped wells. Western Falcon has developed several different proprietary thermoplastics resulting in four unique liners with temperature limits ranging from 160° F to 500° F (71° C to 260° C). Liner applications have also expanded to most forms of artificial lift installations and velocity strings. Downhole tubing internal corrosion and rod on tubing failures are now controlled to the point of making it economical to produce many marginal fields that would otherwise be uneconomical to operate.
Conestoga Supply Corporation is a leading supplier of new, used, and surplus OCTG and Line Pipe. Conestoga Supply is strategically located in the heart of the oil industry with two locations in Houston, Texas and multiple stocking locations in Western Canada.
Western Falcon and Conestoga Supply together are equipped to handle your tubular needs and tubular failure protection requirements in the United States and Internationally. Similarly, Polycore Tubular Lining and Conestoga Supply Canada in Calgary and Bow Island, Alberta Canada services all tubular supply and failure protection requirements for Canada. The Bow Island Facility has been fully operational since June 2007 installing Western Falcon thermoplastic liners and inventory of OCTG for Conestoga Supply in Canada.
Western Falcon’s thermoplastic liner technology eliminates rod on tubing wear in rod pump oil wells and mitigates corrosion in water injection and disposal wells. Through continued product development, technology advancements and flawless customer service, we aim to be the Oil and Gas Industry’s preferred and most trusted solution for all down hole corrosion and tubing wear problems.
Description of Services
The Western Falcon Difference:
- Unmatched Experience
Western Falcon has run more than 70 MILLION FEET (21 million meters) of thermoplastic liners throughout the world. We have the knowledge and expertise to provide a tubular solution for ANY well environment.
- Unbeatable Thermoplastic Liner
Western Falcon’s technologically advanced thermoplastic liners are more robust, flexible and are less expensive than the alternative thermoset coating. This type of liner technology is suitable for all types of well environments regardless of temperature, depth or well type.
- Unlimited Well Type Applications
Our patented liner technology has been designed to solve wear and corrosion issues in both water and producing well bores. It is so flexible in its design, that no longer do you need to run different strings for one or the other. This is an ideal solution for a CONVERSION WELL. This versatility directly translates to less changeover and speaks to its longevity.
- Unconventional Results
Industry leaders in major producing regions around the world are running our technologically advanced liners to reap cost savings, reduce workover downtimes and increase revenue. Don’t be left in the dust.
Western Falcon liner technologies are a proven solution in a wide range of down-hole applications.
Our liners:
- Increase Corrosion Resistance
- Reduce/Eliminate Rod Wear
- Flexible for Water/Producing Wells
- Increase Well Profitability
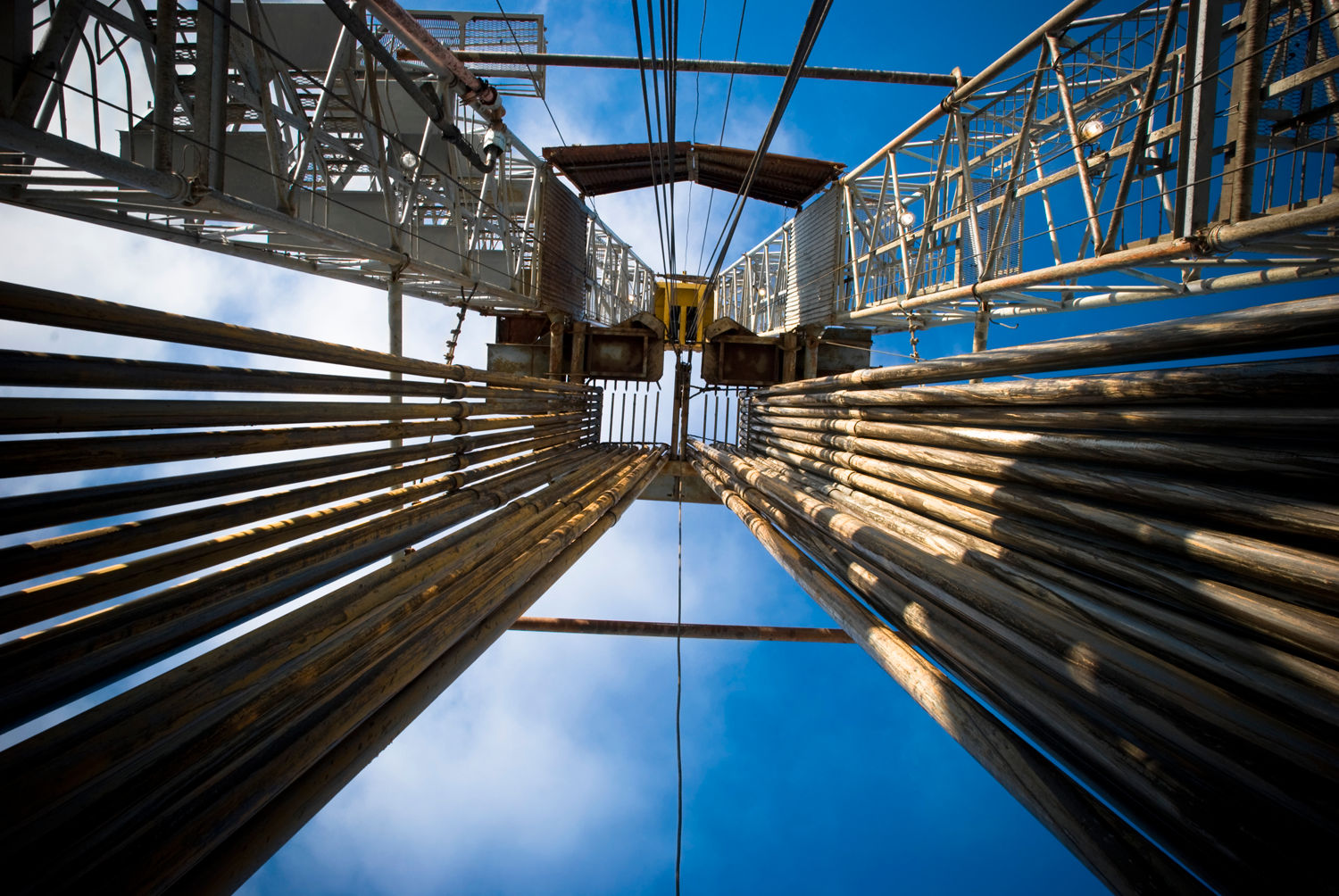
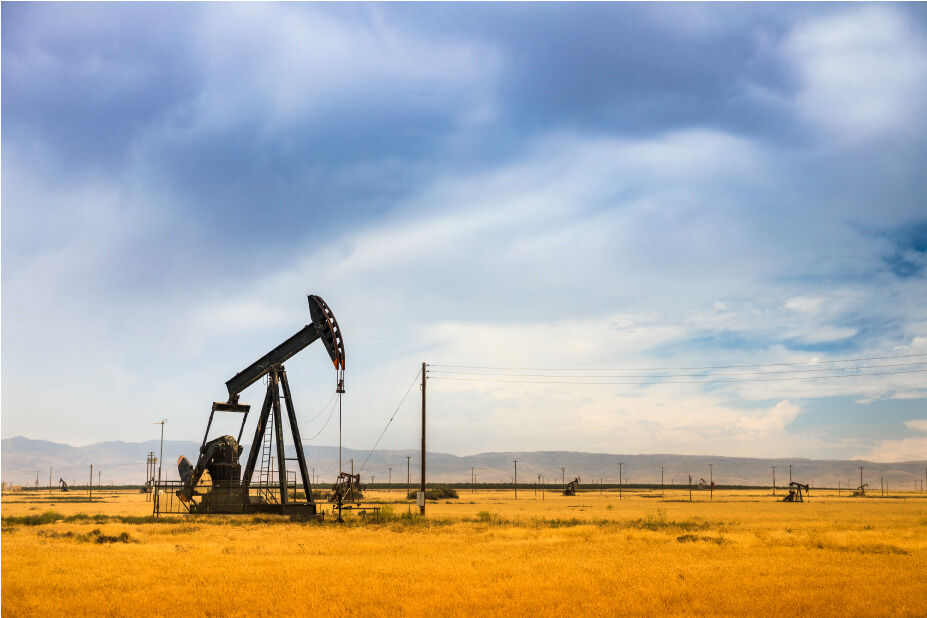
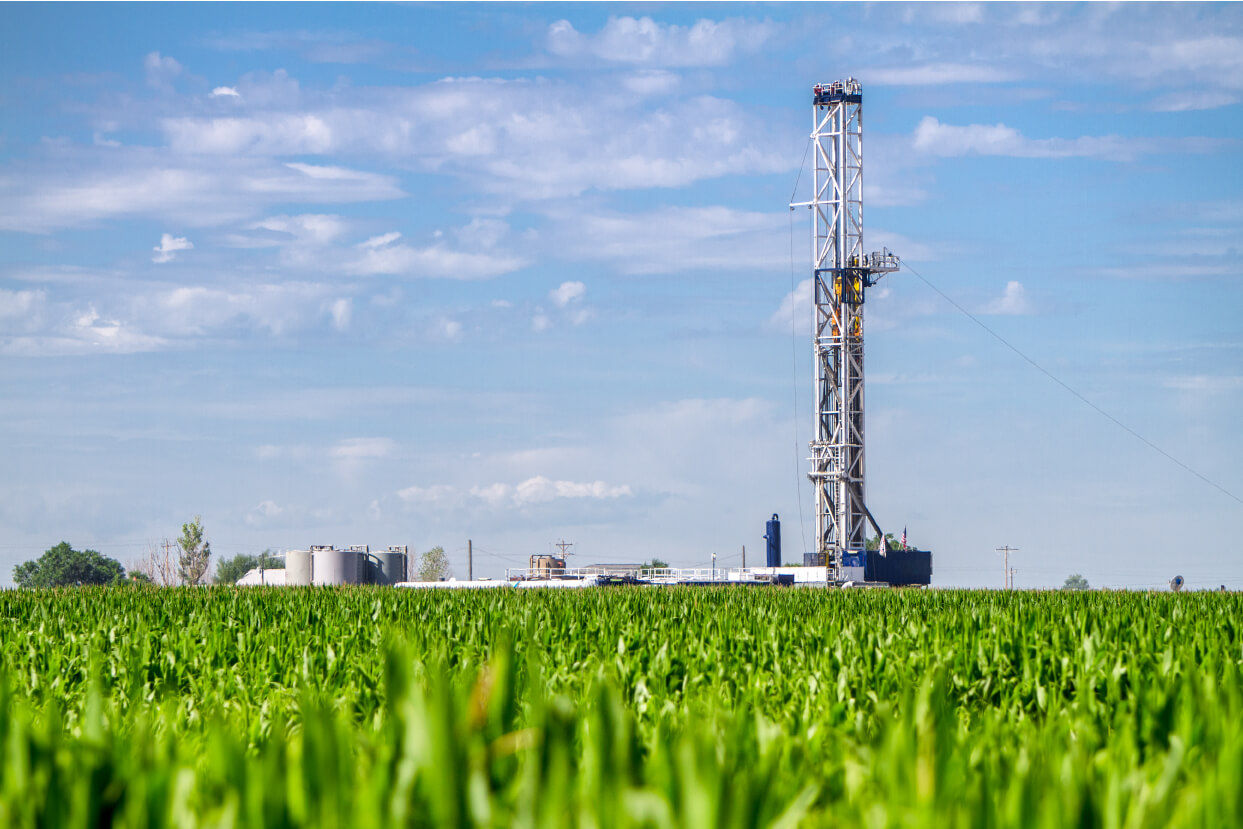
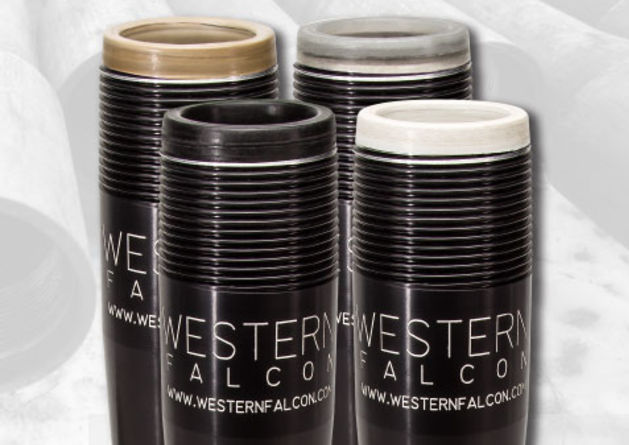
What we do
Our Products Solve Problems:
- Are you pulling tubing before the pump?
- Are you not able to land the pump around the bend?
- Looking to reduce operating costs in your water wells?
- Does your well have a corrosion issue?
- Would you like to see your well economics improve in any market environment?
All Well Environments Are Unique
- Every well environment is unique – with Western Falcon’s wide breadth of success in over 80,000 wells worldwide – we look forward to discussing a solution for you.
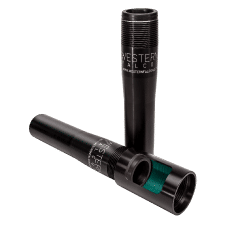
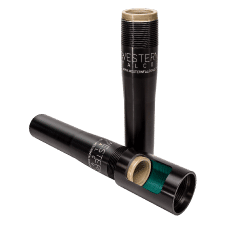
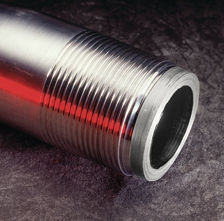
Life at Western Falcon Energy Services
Western Falcon Products:
Western Falcon liners have successfully proven the use of thermoplastic liners in down-hole applications since 1992. Operators are experiencing drastic reductions in operating costs associated with rod-on-tubing wear and tubing corrosion failures. The liner material incorporates proprietary lubricants to aid in mitigating wear and corrosion failures in beam-pumped and progressive cavity pumped wells. Benefits can be realized in highly deviated and dog-legged wells without additional costs for slim hole rod boxes or rod guides. The liners have been equally successful in controlling tubular corrosion in other artificially lifted wells and disposal wells. The extremely smooth liner surface is helping many operators experience decreased pressure drops, electrical cost savings, and increased production due to fundamental hydraulic benefits. The liners have also proven resistant to wire line, acid, and chemical damage. Additionally, a unique mechanical bond allows reuse of used and lower quality tubing saving on steel costs. The bonding procedure allows lining pipe with surface imperfections including the ability to line over damaged used internal plastic coatings without the additional cost of removal. The connection system is the most reliable and easiest to install in the OCTG corrosion control industry.
1). Polycore High Density Polyethylene Liner
Polycore™ is a High Density Polyethylene (HDPE) liner. This patented product is highly abrasion resistant which accounts for its success in the mitigation of rod on tubing wear, wire line, mechanical, and handling damage. HDPE is chemically inert to corrosive materials enhancing its use as a corrosion barrier. The mechanically bonded seamless thermoplastic tube is tolerant to minor surface imperfections of pipe and eliminates concerns with holidays or voids as in adhesive or thermally bonded liners and coatings. Maximum Temperature 160° F (71° C) Oil, 180° F (82° C) Aqueous.
- Polycore™
- Standard Application Solution
- Low-Temperature Rod Pumping Wells
- Low-Temperature Water Wells
- Liner-Compatible with New/Used Steel
2). Modified Polycore High Density Polyethylene Liner
Falcon Modified Polycore™ is a High Density Polyethylene (HDPE) liner. This patented product is highly abrasion resistant which accounts for its success in the mitigation of tubing rod wear, wire line, mechanical, and handling damage. HDPE is chemically inert to corrosive materials enhancing its use as a corrosion barrier. The mechanically bonded seamless thermoplastic tube is tolerant to minor surface imperfections and eliminates concerns with holidays or voids as in adhesive or thermally bonded liners and coatings.
- Modified Polycore™
- Higher Collapse Strength
- Liner Compatible with New/Used Steel
3). Enertube Polyolefin Liner
Enertube™ is a liner manufactured from a specially formulated blend of polyolefins. This liner is similar in mechanical properties to the field proven Falcon Polycore™ liner with a moderate increase in tensile strength and temperature resistance. This second generation of Falcon liners is specifically designed to operate in wells too hot for Polycore™ and is a seamless mechanically bonded liner providing a smooth tubing surface. Maximum Temperature 210° F (99° C) in all services.
- Enertube™
- Higher Temperature Water Wells
- Solution Mining
4). Ultratube Engineering Thermoplastic Liner
Ultratube™ is a high performance liner manufactured from a proprietary blended polyphenylene sulfide thermoplastic resin specially formulated for use in downhole oil and gas production environments. This third generation liner has a significant increase in temperature stability, tensile strength, abrasion and chemical resistance over the other proven liners. The innovative polymers in this liner offer the broadest range of resistance to solvents, steam, strong bases, fuel, and acids. The new polymers are specifically designed to limit (not prevent) the permeability of acid gases such as CO2 and H2S. Maximum Temperature 350° F (175° C) in all services.
- Ultratube™
- Higher Side Load Pumping Wells
- Steam Flood
- Gas Well Solution
5). Extremetube Engineering Thermoplastic Liner for Extreme Conditions
Extremetube™ is a high performance liner for the most extreme operating conditions. This unique liner is made from PEEK Polymer and is the highest tensile strength and highest temperature liner available. Extremetube™ is an excellent alternative to corrosion resistant alloy (CRA) tubulars and offers protection against corrosion and wear problems under the most severe environmental conditions. Maximum Temperature 500° F (260° C).
- Extremetube™
- Offshore Tubing
- Alternative to Corrosion Resistant Alloys
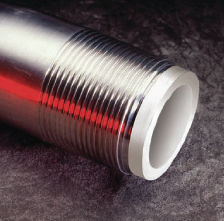
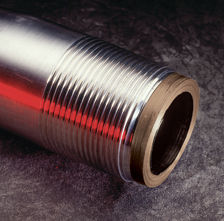