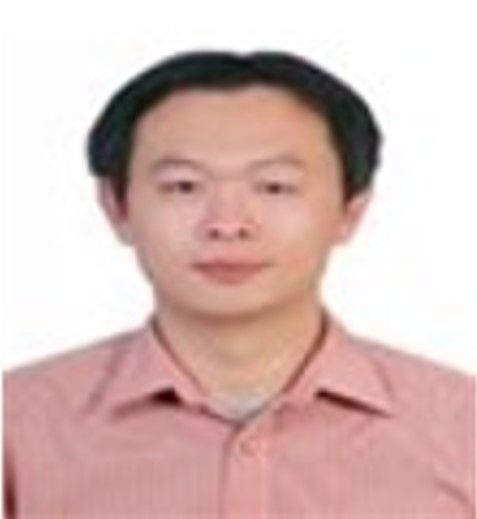
kemp kemp wong
!
About Kemp Kemp Wong
Toufen City, Miaoli County, Taiwan
An overview of the work content of the industry:
The task of working at Daying Zhunan Plant is to assist in the transfer of water-based PU technology and the development and synthesis of coating PU.
The water-based PU synthesis technology selects polyol and low molecular weight two (poly) alcohols according to different characteristics. First, design the equivalent number ratio of OH and NCO. After the temperature rise reaction, a part of the NCO is retained, and then Acetone is used at this stage. The prepolymer is dissolved and reacted with divalent acid groups (-COOH) materials, such as DMBA, DMPA, etc., to make the Prepolymer have a part of acid groups and then ionize with triethylamine, etc., and then contain divalent Chain extension etc. in pure water of amines.
The synthesis technology of coating PU is roughly the same as that of water-based PU, and the difference is solvent-based toluene, xylene, IPA, MEK, etc. After obtaining the NCO% retained by the first-stage reaction from the theoretical amount and the actual titration value, proceed to the second-stage reaction. Introduce different types and ratios of alcohol amines and pay attention to their viscosity-increasing properties to avoid excessive viscosity-increasing gel or alcohol Excessive introduction of amines results in failure to increase viscosity, etc.
The main task of Lida Chemical, which was invested and established by Dainippon Ink (DIC) in Taiwan, is related to the synthesis of organic polymers.
Including: development of various types of UV-curing resins, including water-based UV synthesis of UV-curing resins, Epoxy acrylate Oligomer, Polyester acrylate Oligomer, Polyurethane acrylate Oligomer, and the development of UV resins combined with nano sol-gel to achieve higher physical properties and the subsequent oligomerization It can be mixed with UV monomer to obtain resin performance that can not be achieved by using UV monomer alone, so as to improve the surface UV film physical properties of various 3C products, PET film, PC film, hardware, etc. after light curing, and photosensitive development type circuit New ink project and new project development of new PSPI.
UV light-curing resin synthesis includes: development of various types of UV-curing resins, including the development of UV-curing resin water-based UV synthesis, Epoxy acrylate Oligomer, Polyester acrylate Oligomer, Polyurethane acrylate Oligomer, and the development of UV resins that combine with nano sol-gel to achieve higher physical properties. It is mixed with oligomer and UV monomer in the latter stage to obtain the performance of photoresist material that can only be achieved by using UV monomer alone, so as to improve the physical properties of various 3C products, PET film, PC film, and other materials after photocuring.
The water-based (Pressure Sensitive Adhesives, PSA) pressure sensitive adhesive synthesis process can be divided into two methods. The first method is to use Acrylate monomer as a raw material to select different acrylic monomers with preset coating performance and adjust the temperature of the water bath according to the required average molecular weight distribution. Commonly used initiators in emulsion polymerization are APS and SPS (aqueous initiators). After preemulsion, the Acrylate monomer needs to be maintained for more than 40 minutes without stratification, and then it is poured (dropped) into the reaction tank in proportion to the aqueous initiator to adjust the stirring speed (slow), and the whole reaction time is adjusted and then matured. The other is the hybrid method of emulsion polymerization.
The Acrylate monomer for solvent-based Acrylate (Acrylate polyol) polymerization (polyol is introduced into β-H, 2HEA, etc.) is roughly the same as the raw material of water-based Acrylate. The other is that the solvents such as Tol, Xyl, PGM, IPA, etc. are adjusted to meet the requirements according to different resin uses and the design of the reaction temperature. The higher the oil bath temperature of the reaction, the lower the average molecular weight, and the lower the oil bath temperature, the higher the average molecular weight. Commonly used initiators (catalysts) include AIBN, PO, PZ, PD, BPO, etc., and different initiators and amounts are selected according to different reaction temperatures. The dose of the initiator is also the key to adjusting the average molecular weight. The lower the input amount, the larger the average molecular weight, and the larger the starting agent input amount, the smaller the average molecular weight.
Epoxy acrylate Oligomer is adjusted according to different uses or performance of the use. The difference between the equivalent number, equivalent weight and valence of the raw material to be reacted is converted into the actual reaction amount (weight). Epoxy monomer (usually solid) and acid glycosides and acids Compounds (MAA, AA), etc. are synthesized through additional reactions, and the acid value is monitored to the end of the reaction Cut.
The synthesis method of Polyester acrylate Oligomer is based on the formula F-OH = Mn * OHV / 56100, OHV = (E OH- A)*56100/Yield, Mn = W / E mole-E A and other formulas. Two or more raw materials with hydroxyl (-OH), such as: NPG, DEG, DPG, TMP, etc. And use two or more functional group materials or acid glycosides with acid groups (-COOH) to introduce unsaturated bonds (π bonds) through the double bond in the molecule. Raw materials such as: AA, THPA, Man, FuA, etc. The reaction input is followed by the first alcohol and then the acid method to reduce resistance and easy dispersion during the initial heating and stirring. Then calculate the amount of catalyst input (in ppm) based on the total amount of solid input, and increase the temperature in order to reduce the amount of alcohol loss for polymerization. Condensation dehydration reaction and monitoring acid value, cut to the end of the reaction.
The synthesis method of Polyurethane acrylate Oligomer is to design the NCO/OH equivalent ratio of the formula first, and the temperature is controlled by acrylate monomer with hydroxyl (-OH) (generally with multiple π bonds) and isocyanate (IPDI, HDI, TDI, etc.) React to within the preset NCO% specification value, and then perform the back-stage reaction according to the monomer raw materials for different functions and purposes until NCO% = 0, and finally adjust the viscosity, solid content, and filter press.
Photosensitive and developing circuit inks are divided into two types: soft board and hard board. The common point is that the synthesis method is roughly the same, and the difference is that the types of raw materials are slightly different and the monitoring points are different.
The soft board has solid content: 50-60%, solid acid value: 50-80mgKOH/g, viscosity: ≦30000cps, and has good adhesion to PI and copper foil and has flexibility.
The rigid board has solid content: 50%, solid acid value: 90~110mgKOH/g, molecular weight: about 30,000 and has good compatibility with epoxy resin and
Good finger touch, etc.
The new PSPI (Photosensitive polyimides (PSPIs)) project is based on the traditional PI synthetic base and introduces photosensitive inks synthesized by monomers with light curing conditions. After coating it under the initial heat drying and mask (Mask) and curing with UV light, it is developed with its own carboxyl group in alkaline aqueous solution, and then heated and hard-baked to close the loop... etc.
The main task of Silicon Technology in Taiwan is the development of organic silicon.
Overview of organic silicon development, the work content is divided into two major projects:
One is the development of more physical properties: HTV (High-temperature vulcanized silicone rubber) hot vulcanized silicone rubber and LSR (Liquid Silicone Rubber) liquid silicone rubber materials related formulations.
The second is the development of more chemical properties: the synthesis and modification of organosilicon resins (M/Q resin, hydrogen-containing functional silicone oil, development of related resins after PU modification and HTV thermally vulcanized silicone rubber, Acrylate modification and HTV Development of related resins for thermally vulcanized silicone rubber bonding, development of organic silicone hand-feeling oil synthesis, development of primer and silicone oil synthesis with bonding of dissimilar materials, POSS synthesis (Polyhedral Oligomeric Silsesquioxane), platinum catalyst synthesis and activation followed by coordination inhibition for HTV heating Addition of vulcanized silicone rubber...
Outline the above two major projects
HTV thermally vulcanized silicone rubber is made of raw silicone rubber that is uniformly mixed with hydrogen-containing silicone oil, platinum catalyst and related additives, and then molded by physical methods such as molding or calendering, and then vulcanized (cured) molded at a certain temperature and time. The application is mainly through adding Silica powder, alumina powder, carbon black, white carbon black... and other materials with thermal and electrical conductivity, foaming or special functions in the HTV glue to give its functionality through vulcanization molding. .
For example: ACF Anisotropic Conductive Film (Anisotropic Conductive Film), which can conduct electricity and heat, and has both cushioning and pressing effects and good release properties. It can be used for repeat applications in the process. Another major composite cushioning material (solid silicone and glassfiber-reinforced) is a special base material with fatigue resistance, tensile strength and tear strength, and excellent flexibility.
LSR liquid silicone rubber is mainly divided into two agents: A/B. Agent A generally mainly contains inhibitors, platinum catalysts, large molecular weight vinyl silicone oils, etc., and agent B generally contains large molecular weight vinyl silicone oils, hydrogen-containing silicone oils, inhibitors, etc. . In the application, the A/B two agents are stirred by mechanical force or the solvent is added to dissolve the two agents to dilute the application...
Organic silicon resin synthesis and modification M/Q resin Its function is mainly used as the main component of PSA organic silicon pressure sensitive adhesive synthesis. M refers to hexamethyldisiloxane and divinyltetramethyl with end-capping effect. Disiloxane, tetramethyl disiloxane, Q generally refers to TEOS (tetraethoxysilane). Synthesize different M/Q resins with molecular weights from large to small (solid→liquid) through different ratios of M/Q. Because it has a part of the three-dimensional structure Cage, it has the strength to improve the degree of solid silicone (Strengh) With the effect of tearing, the active end M (divinyl tetramethyl disiloxane, tetramethyl disiloxane) can introduce different functional functional groups (groups) to produce different Other applications in the field.
The function of hydrogen-containing functional silicone oil is mainly used as HTV silicone rubber crosslinking agent. It is a high molecular weight silicone oil purchased from outside for molecular rearrangement and equilibrium reaction or is based on the basic raw material D4, hexamethyldisiloxane, divinyl Tetramethyldisiloxane, tetramethyldisiloxane, tetramethylcyclotetrasiloxane D4H, through the organic synthesis equivalent, equivalent number design and calculation, the neutralization after the cation balance reaction is a kind of crosslinking Functional silicone oil.
The introduction of different functional groups (groups) in the synthesis of cross-linked silicone oils can produce functional silicone oils with different bonding of different materials. Almost all materials (except fluorine materials) have been overcome, such as: PC (polycarbonate), carbon fiber board and cloth, glass fiber products, polyester fiber, cotton-containing polyester cloth, Kevlar fiber fiber), polyimide (PI), polyethylene terephthalate (PET), carbon fiber (board), glass... etc.
After PU modification, it is bonded with HTV heat vulcanized silicone rubber, and after Acrylate modification is bonded with HTV heat vulcanized silicone rubber. Special coatings are used to modify the surface properties of the solid HTV silicone rubber (smoothness, release, hydrophobicity, Hydrophilic.. etc.) a surface modified resin.
Organic silicon feel oil synthesis It is a functional synthetic resin with hand feel and release by self-synthesis and then coated
A surface modification of HTV heat-vulcanized silicone rubber, which is difficult to coat.
POSS synthesis (Polyhedral Oligomeric Silsesquioxane) is a special oligomer produced by hydrolysis-condensation of Silane, which is generally sold on the market, because it has a special structure of "half-half" and can be used in all industries. Because of its particularity, it has a cage structure inside and has a buffering function. Different functional groups hang on the outside. It has different functions for the grafting, modification and strengthening of polymers, and its exposed functional groups can be extended. Different functional groups are grafted to produce different application fields...
There are currently several POSS oligomers that have been synthesized in small quantities to:
https://hybridplastics.com/products/rd-chemicals/ and
http://www.mayaterials.com/q8-products The products on these two websites are breakthrough targets.
To summarize the above; that is, the oligomers or polymers with active units after self-synthesis are collected and then formulated and kneaded through a rubber mixer (two rollers) and solid silicone rubber are subjected to strong shearing and physical kneading, and then kneading. The samples are compressed by a molding press and dissimilar materials to produce composite materials with different thicknesses or different layers, and then heat vulcanized to form and post cure.
Take the post-cured samples for various performance tests, including Shore hardness, thermal and thermal shock test and adhesion, tensile testing machine (tensile strength, tear, elongation test), surface roughness, electrical and thermal conductivity, etc....Sampling customers and Feedback.
When serving in the industry, because it is in the research department, the company's technology know how is due to competitive factors, the above is only presented as an overview.
Education
University:Since the electro-optic technology is developing vigorously, the design of electronic products is becoming more compact, such as DVD players and digital cameras. In order to achieve smaller size and lighter weight, micro elements need to be developed, such as microlens arrays and diffractive optical elements. Microlens arrays are among the most widely used optical components, which are used in display components, optical sensors, wireless communication, and optical fiber communication. Conventional production technologies can no longer meet the demand for producing precise micro elements, thus, a replication molding technology for mass production of precise micro components is urgently needed.
This study developed creative imprinting technology, combining nano-imprint lithography and array-type UV-curing technology. It used nanopowders as the method to transmit imprint force, and integrated technical features, such as soft lithography, light-curing resistant and gas-assisted imprint technology, in order to study the development of technological processes of micro-lens array manufacturing, and mature the application and technology of nano-imprinting. According to research results, SUS 304 stainless steel sheet with a micro-hole array could be smoothly fabricated into an original micro-lens array mold upon gas-assisted micro-hot embossing. At the same time, a micro-lens array structure with a complementary external form could be precisely remolded and reproduced by PDMS. Complete molding of micro-lens could be effectively achieved by combining imprints of gas-assisted lithography developed in this study, and even UV-NIL. The effective imprinting area and reproducibility of transfer printing could be greatly improved when a micro-lens contacts perfectly with a substrate surface. Moreover, since PDMS soft molds have short remolding times, and are easily feathered during manufacturing, production costs could be effectively reduced through features such as, low surface free energy, resistant to adhering to the mold during imprinting, and collocation of gas-assisted nanopowder imprinting of micro-structural processes.
Work History & Review
No Work History & Review yet!